Manufacturing margins: 5 ways to protect your bottom line
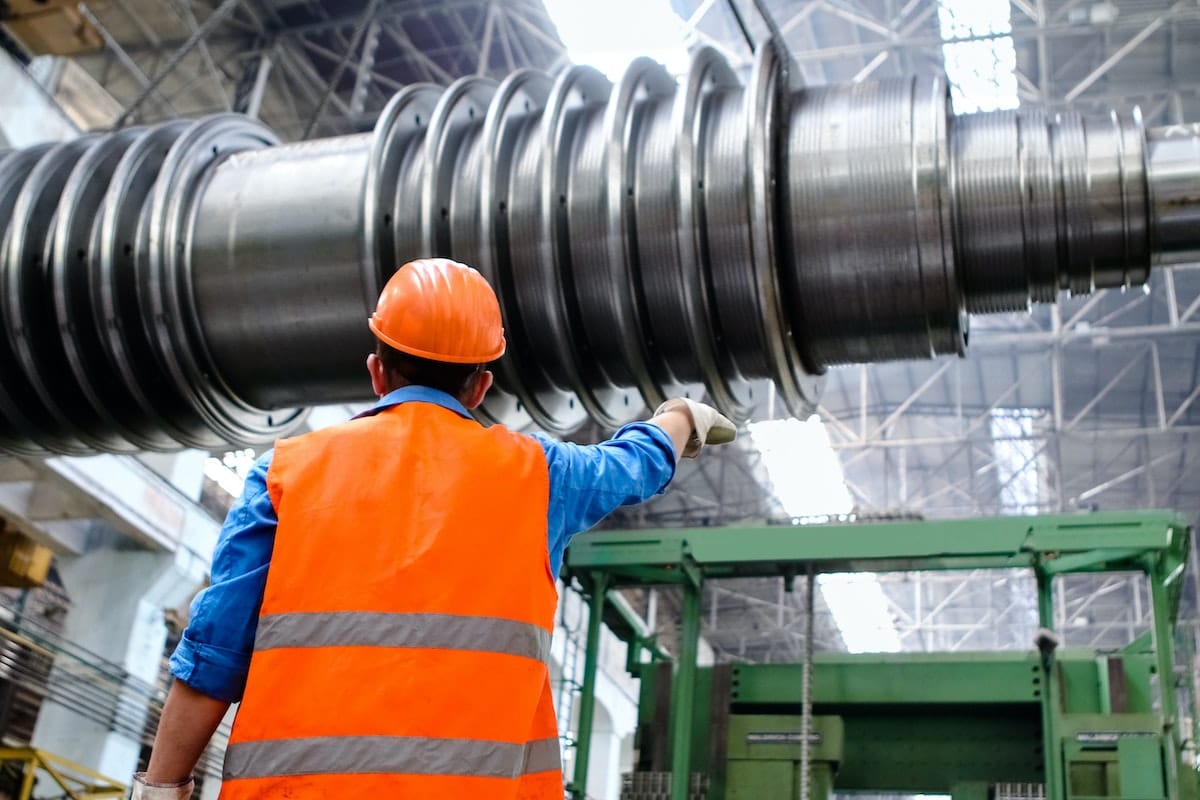
The COVID-19 pandemic — and the lockdowns it prompted — caused huge upheaval in almost every supply chain.
Add in economic uncertainty and rising inflation, and you have something of a perfect storm for the manufacturing industry.
Yes, a lot has changed over the past few years. But the smartest manufacturing companies are learning to stay nimble and roll with the punches, and it’s helping them to not only survive, but thrive.
Let’s take a look at what some business leaders in the manufacturing industry are doing in these changing times to help protect their bottom line.
What has changed in the manufacturing industry?
Maybe we’d be better off asking what hasn’t changed in the manufacturing industry. The COVID-19 pandemic affected every aspect of the production process.
Demand plummeted. Supply chains broke down. Workers quit. And some plants were temporarily shuttered.
At one point, US production recorded the largest monthly drop since the Second World War.
But, the good news is that things are looking up.
The manufacturing industry is beginning to show some notable signs of recovery. Revenue is rising for many companies, as industrial production and capacity utilization surpass pre-pandemic levels.
Nevertheless, there are still a number of key challenges facing the manufacturing industry. These include:
- Labor shortages: It’s becoming more costly to retain and attract the staff a business needs to operate reliably
- Supply chain challenges: Manufacturers are missing out on revenue as they fail to fulfill orders on time
- Increased costs: Inflation is raising costs across the board, from fuel to parts to energy
- Economic uncertainty: Investing in the future feels tricky at a time when the economic outlook is still uncertain
All of the above stand to affect the revenue of any manufacturing business. But there are things you can do to counteract these effects.
5 ways to protect your bottom line
Change your supply chain strategy
Unfortunately, supply chain instability looks set to stick around for a while. So, in order to protect their bottom line, manufacturers have to find a way to adapt to it.
This means analyzing, improving and diversifying the supply chain.
Reshoring — doing business with at least a few partners closer to home — improves diversification. By reducing the distance between the links of your supply chain, you reduce the chance of disruption.
When it comes to improving the process, manufacturers are questioning old ways of doing things.
Just-in-time inventory management just isn’t as feasible when you can’t rely on timely deliveries. So, time margins are increasing to help companies better cope with the unexpected.
Utilizing modern technology is also a great way to hone supply chain operations.
When you — and your partners — have access to real-time inventory data, it’s easier to anticipate supply chain snarls, and act quickly in response.
Harness the power of technology
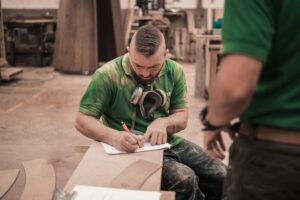
The right tech can revolutionize the way you do business by streamlining and even automating day-to-day processes.
Investing in tech solutions to perform manufacturing tasks and provide operational data is a wise move.
Why?
Because tech helps manufacturers to keep their company competitive.
You get to boost your bottom line with the help of connected, reliable, efficient and predictive processes at your manufacturing locations.
Roll out tech tools to your partners too and you join the dots, sharing important data and allowing everyone to take preventative action when things aren’t going to plan.
Improve employee retention
Faced with a labor shortage, many industries — including manufacturing — are finding it even harder than usual to source the staff they need.
This makes it much more difficult to cope with the recent uptick in orders that many firms have been experiencing since the end of last year.
The answer? Do your best to hang on to the people you’ve already got.
We are in the midst of the Great Resignation, and employees are more aware of what they want — and need — in a job than ever before. Many manufacturing firms are losing employees to better positions elsewhere. The solution? You need to make your positions more appealing.
To improve employee retention, you might choose to:
- Raise wages
- Offer additional perks
- Provide training opportunities
It’s also important not to overlook well-being — almost half of workers are prepared to move to a new organization to improve their well-being. This may be through flexible working opportunities, investment into company culture, or reexamining current stressors in the workplace. A recent study suggested that job-specific stress within the manufacturing industry included high job demands, low job control, the ergonomics of the work environment, and unrealistic work patterns and schedule.
There may not be easy fixes to each of these, but there are practical solutions employers can implement to make them less stressful. For example, when employees must travel or visit a remote job site, providing comfortable accommodation helps your workers get good sleep and relax at the end of the night. Using a service like Hotel Engine makes it easier and more cost-effective to provide business lodging that will keep employees happy.
Think about sustainability
While survival has been the priority for many manufacturing businesses over the past couple of years, as we exit the pandemic it’s important to look to the future.
Sustainability is a pressing concern for the manufacturing industry.
We can expect to see more environmental, social, and governance (ESG) legislation from the government, and scrutiny from partners and customers too.
Protect your bottom line by getting ahead of the curve. Examine and optimize sustainable and carbon-neutral practices to prepare your business for what lies ahead.
Reassess your partner relationships
When money is tight, you have to trim the fat. With the prices of energy and raw materials rising, you have two options: Reduce costs, or resort to passing them on to your customers.
There’s never been a better time to reassess your partner relationships and the contracts you have in place.
Can any savings be made? Is there room for renegotiation on any existing arrangements?
Do contracts take into account today’s price volatility? Do they allow you the agility you need to respond to changes in demand?
As well as examining the partner relationships you already have, now is also a good time to build new ones — particularly if those partners can help you to reduce costs across the company.
Consider travel: Manufacturing and business travel go hand-in-hand. In fact, the industry spends approximately $10 billion annually on project-based travel. These costs account for supplier meetings, touring production plants or potential locations, research, and engaging with customers or prospects. A service like Hotel Engine could make your employee accommodation more affordable and efficient.
How Hotel Engine can help protect your bottom line
Travel costs for manufacturing businesses with a traveling workforce can quickly mount up, not to mention the hours spent by your workforce on booking, managing and billing for those reservations.
Hotel Engine is a hotel booking platform built for businesses. Our customers can save up to 60% on lodging and get access to easy-to-use tools that allow you to track and analyze your travel data, learning where you’re spending your money — and where you can make savings.
Ready for the best part? Hotel Engine is completely free to use — no booking fees, no contract, no minimum spend.
It’s one smart thing you can do to start protecting your bottom line today.
To get started, sign up for your free account here.